Understanding the Benefit of Customized ControlLogix Training
Obviously, the main Benefit of Customized ControlLogix Training is reduced downtime. Unknown conditions greatly increase troubleshooting time when solving a problem. When your technicians don’t know what is causing a problem, they may be randomly checking switches. They are randomly wiggling wires on your system. They are hoping that the issue will suddenly reveal itself.
On the other hand, a well-trained technician will be able to follow a procedure for troubleshooting. This procedure allows them to narrow down any problem quickly. Imagine that you have a cylinder that will not extend. This part of the process is preventing your equipment from completing it’s cycle. Students who attend a training course will have the knowledge to determine if the processor is even calling for the cylinder to extend. If so, then they will learn how to use the schematics to trace down the problem.
Likewise, if the processor is not calling for this output, they will learn how to navigate through the logic. This allows them to find out what condition is preventing this output from energizing. This could be an alarm condition, or a simple limit switch the processor is not seeing. The key of course is to find the condition first. At this point, they can go back into the machine schematics. After that, they can trace down why the switch is not getting a voltage to the input module.
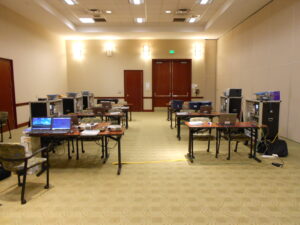
Understand the Instructions
When troubleshooting, your employees will come across various instructions in the processor’s program. In order to understand how the system is working, they will need to understand how these instructions operate. There are various types of digital input and output instructions they will encounter. These include standard outputs, latches, and one shot instructions. Additionally, your project likely involves timers, counters, and analog instructions. By understanding these instructions, your technicians will be able to determine what needs to happen for your outputs to energize.
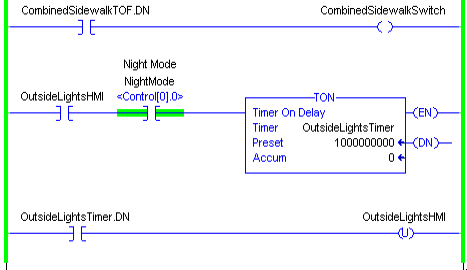
Project Navigation
Once you find an output that will not energize, we just need to look at the conditions before that output. This will tell us why the output did not energize. It would be nice if all of the conditions were on the same rung, but this is almost never the case. In reality, the rung will have internal bits (coils) that we must trace down. Each of those could lead us to several other internal coils to trace down. Students who attend training will learn how to use the ControlLogix Bookmark system, and cross reference features. This allows you to navigate through the program to find out the reason your processor is not calling for an output. The training will give you plenty of practice with these features. In effect, you will able to quickly navigate your own plant projects to find the root cause of failure.
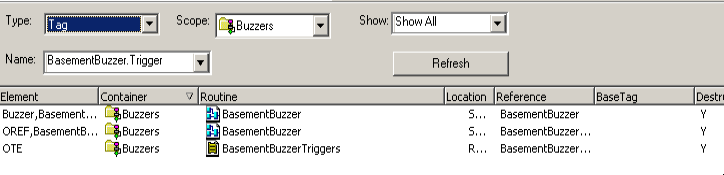
Other Troubleshooting Tools
Students will learn to use other troubleshooting tools such as trending, the quick watch window, and how to create “Traps” in your project. Trending allows you to graph analog (or digital) signals over time.
On the other hand, the quick watch window allows you to monitor specific tags in your program. Basically, if an output won’t energize, students can create a quick watch window for that particular output. This quick watch window can contain all of the conditions we require to energize the output. The next time this failure occurs, the technician can just bring up the quick watch window. At that point, they can just look down the list to see what conditions are not made, and go right to the problem.
Students will also learn how to create “traps” in your project. Imagine a machine that continues to shut down intermittently throughout the day. You might suspect an intermittent problem on a safety gate is the issue. The technician can simply add a counter (or latch) to each safety gate. The next time the problem occurs, they can simply look at which counter incremented. This will tell them which gate is causing the issue.
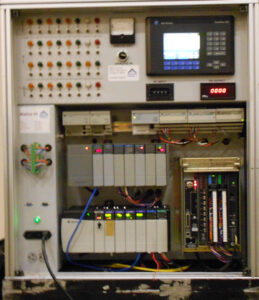
Summary of the Benefit of Customized ControlLogix Training
In short, downtime is expensive. When students are trained, they can quickly locate issues in your equipment. Additionally, they will gain confidence in knowing that they have the ability and knowledge to troubleshoot each part of your system. The ControlLogix processor will no longer be an unknown part of the troubleshooting process. Your students need training that applies directly to what they need to know to troubleshoot your own plant systems.
For more information on ControlLogix, visit the Category Page!
— Ricky Bryce