Introduction to ControlLogix PID Training
ControlLogix PID Training allows the students to understand certain areas of Process Control. PID is Proportional, Integral, and Derivative. For example, we have a heating system. The goal is to maintain a constant temperature. Good PID control returns the temperature back to the set point quickly. This should happen even under various load conditions. With PID Training, we’ll look at P, I, and D individually. Students will understand how the controller calculates output for each component. Additionally, they will learn how to troubleshoot and tune a PID loop. Other examples of PID control include pressure and flow control loops.
In class, we will use a hardware simulator. This connects directly to the analog I/O modules. The simulator allows the students to simulate various processes. They will be able to adjust lag, load, process delay, and noise. By varying the settings, they will also practice tuning loads with different process dynamics.
We will base this training on your own processes. In class, we’ll use your own plant programs as examples.
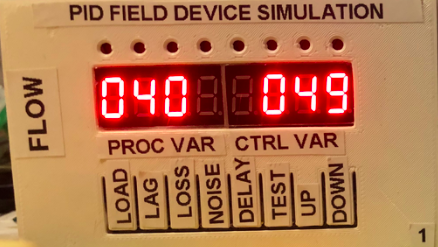
Analog I/O
Before we begin training with PID, students must understand how to configure analog modules. They will also learn various methods for scaling analog data. For many analog modules, the controller receives raw data. We must scale this data into engineering units. On the other hand, some modules, such as the 1756-IF16 support on-board scaling. The advantage of these modules is that the analog module does the scaling. This frees processor time and memory. By using real analog modules, students will gain a full understanding of the entire loop. This even includes noise on the feedback that will give students a feel for what they will actually see in the plant!
Proportional
The controller bases output from this control on error. In other words, the more error we have, the more output we have. It also bases the output on tuning parameters. The more gain we have, the more output we have from the controller. However, if the gain is set too high, the loop becomes unstable. In class, students will learn how to find the correct value for proportional gain. Additionally, they will learn how to troubleshoot a loop with too much proportional gain.
Integral
In a heating, flow, or pressure control system, proportional gain alone is not enough. We cannot maintain the set point. By using integral, the processor continues to add to the output over time. Generally, this happens as long as we are below the set point. As the error becomes less, the controller adds less to our final output. In class, students will learn to find the correct value for integral. Not only will they learn to find the correct value, but also they will be able to troubleshoot an incorrect integral gain.
Derivative
Although we don’t always use derivative, it is valuable when needed. Derivative works by looking at a rate of change. For example, if an oven door opens, the temperature suddenly drops. At this point, the derivative would see a high rate of change, and increase the output to compensate. Students will lean when to use derivative. They will also learn about the problems they will encounter when this setting is incorrect.
Feed Forward
Basically, this is the opposite of feedback. This provides a bias to the output even before the feedback begins to change. For example, we have a heating process. If product flow increases by 50%, we can immediately bias the output by 50% (or any scale of that). Not only will we reduce deviation from the set point, but we will also achieve the set point much faster.
Deadband
Deadband eliminates control action when your feedback is near the process variable. This can reduce control action. For example, if you have a pressure control process, it can reduce wear on a valve if it’s set up properly. An improper deadband setting will cause the loop to become unstable. Students will learn how to set up deadband on a controller, and learn the difference between zero crossing and non-zero crossing control.
Tuning PID
Students will practice tuning many PID loops with different process dynamics. We’ll use both the heuristic method for tuning, and the Zieglar-Nichols method. Basically, with the heuristic method, students will run the proportional gain up until the loop becomes unstable. At that point, they will record the natural period of the oscillations. We’ll use the values we record to set the gains for the PID loop. Likewise, with the Zieglar-Nichols method, they will learn how to open the loop, and record various dynamics such as lag, integration rate, gain, and time constant. We’ll use these values to find the final gains which make the loop both fast, and stable.
Cascading PID
Each training station will have two hardware simulators. This allows us to teach cascading PID loops. In this case, one PID controller writes to the setpoint of another controller. A good example of this would be for a tank level. A PID controller monitors a tank level, and writes a setpoint to a flow controller. This allows the primary controller to maintain the tank at a constant level. Since tanks are integrating processes, we’ll need to use a special formula to tune the tank level. Once the students understand how to tune the tank level, we’ll apply Feed Forward, which will send the load request back to the primary controller. This drastically improves the response time of your closed loop system.
Platforms and languages for ControlLogix PID Training
Students will learn the difference between ladder logic PID, and function block PIDE. They will have a chance to configure both. Ladder logic is position based PID, and function blocks provide a velocity based PIDE instruction. Additionally, we’ll cover manual and automatic control of each type of PID instruction. If you use PlantPAx, then we will cover this as well.
Summary of ControlLogix PID Training
To summarize, students will learn how each component of P, I, and D work. They will also learn how to tune a PID based on the heuristic method, and algorithmic method by performing step changes to a process. They will learn how to tune a PID for a fast response without the loop becoming unstable. At the same time, if a loop is unstable, they will learn how to identify and troubleshoot the incorrect tuning parameter, or failed hardware device.
For other information on the ControlLogix system, please visit the category page!
— Ricky Bryce