Introduction to Customized System Training with ControlLogix
Customized System Training with ControlLogix uses your own schematics, and your own programs to TRAIN your students. If you are sending students to seminar-type training, then your students may not be getting the most out of the class.
Your plant programs are proprietary. Since not all students at a training seminar are from your company, the instructor cannot use your own plant materials. Additionally, the instructor cannot vary from a pre-determined outline. For this reason, your students end up with standard, canned information that may or may not apply to what they need to know.
An instructor experienced with customized system training will tailor the class to fit your needs before the class. Additionally, an experienced instructor will modify the course on the fly to ensure the course stays in line with your training needs.
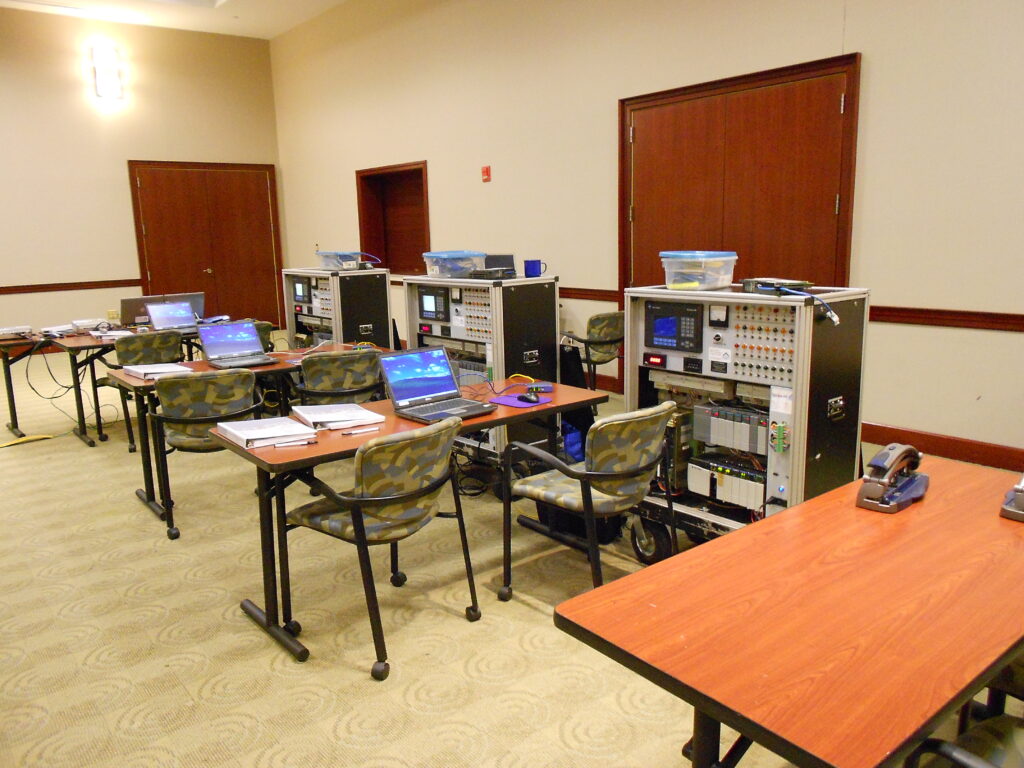
Advantage of Customized Training
Your own plant documentation is the training material (in addition to our training workbook). Students will learn how to troubleshoot equipment based on your own schematics and plant programs. The instructor will show the students how each topic covered in the course applies directly to what they need to know. Additionally, students will practice tracing down real outputs in your own programs to learn the reasons why field devices can fail. During this training, the instructor uses the Socratic training method, directly asking questions to individual students, keeping them engaged. A series of questions will lead them to the correct answer. This also seeks out possible conceptual errors in their knowledge. Each individual in class is a highly respected customer.
What we cover in Customized System Training with ControlLogix
Hardware
Using your own schematics, students will understand the hardware in your own systems. They will learn what the status lights indicate, and how to trace down failures on your own field devices. They will also learn how to replace failed modules, flash firmware, and set IP addresses in devices such as drives and Ethernet modules if necessary.
Communication
Students will understand the communication path between your troubleshooting terminal (RSLogix / Studio 5000), and the processor. They will understand how to build a communication path to go online with your processors.
Basic Instructions
These are the building blocks of all logic Students will need to navigate through the program to find failures. As they navigate through the program, they will come across many instructions. They will need to understand the purpose of each instruction. This leads them to figure out which field device failed. It’s important to realize, the problem is not generally with the program itself. They are simply using the program as a troubleshooting tool to figure out which field device failed.
Timers and Counters
Timers will delay certain parts of your equipment from moving, or from shutting off. They will likely encounter many of these timers while navigating through your logic. Therefore, they must understand the purpose of a timer, and how the bits operate. Counters, on the other hand are not just good for keeping track of a product. They are very useful in troubleshooting too. Students will learn how to use counters as “traps”. This will help them to solve intermittent issues with your equipment.
Analog Signals
Generally, your equipment will have various analog sensors for pressure, temperature, etc. Occasionally, an analog sensor, or it’s wiring connections will fail. Students will learn how to trace down these analog signals to the input or output channel on an analog module. After that, they will use the schematic to trace down the wiring connections. This allows them to determine whether the sensor, module, or wiring connections caused a failure.
Troubleshooting Tools
Students will learn about various troubleshooting tools they have available. This helps them to determine the root cause of failures in your system. These troubleshooting tools include Trending, Cross-Referencing, Searching, Bookmarking, and the Quick Watch window in RSLogix / Studio 5000.
Summary of Customized System Training with ControlLogix
In short, this is not a standard watered-down ControlLogix course. Students will learn exactly what they need to know about your own ControlLogix System. This will fill in their gap of knowledge when it comes to ControlLogix. When they understand all parts of your industrial systems, they will gain confidence in troubleshooting. Additionally, they will be able to solve programs more quickly. This leads to decreased downtime, and increased profits! As one customer stated, “If you are frustrated with standard training, then this class is like a breath of fresh air!”.
Click here for a quote on this training course.
For more information, visit the ControlLogix Category Page!
— Ricky Bryce