How to fix PIDE Stuck High or Low in ControlLogix
Using Function Blocks in ControlLogix, you can get the PIDE Stuck High or Low. This can occur when you are tuning a loop. To begin with, you only have proportional gain when tuning the loop. Your Process Variable could be saturated high or low. No amount of proportional gain will cause it to change. This is because PIDE is velocity based.
The changes to your proportional gain only apply to the change in error or process variable from that point on. Obviously, since the process variable is not changing, your gain changes will have no effect. It’s a “Catch 22”. To begin tuning the PID, we really want to see the process variable somewhere near the setpoint.
In this post, I’ll go over some methods for solving this problem. This will allow you to begin tuning the PID loop.
Disclaimer
It’s important to realize that these are just the methods that I use personally. Remember that these methods are only for resolving a stuck PV when tuning a loop from scratch.
Basically, these will be “trial and error” methods since we don’t know the final tuning parameters yet. Using any of these methods could cause your loop to become unstable. Find someone experienced in PID to help you if there is a danger of damage to equipment or people!
Apply Feed Forward (Bias)
One option is to apply some amount of bias to the control variable. The Feed Forward (FF) will directly change the value of the control variable. Keep in mind that some processes are reverse acting. This means that you must increase the Control Variable to increase the Process Variable. On the other hand, you will have some processes that are forward acting. In this case, you would increase the Control Variable to drive down the Process Variable. Find a value that puts your process variable somewhere near the setpoint, so you can start tuning. Once you find a good value, you will need to leave the FF set until you are finished tuning the loop (or at least until you have integral set up correctly).
An easy method to change the FF is to go to the setup screen. You will find the setting on the “Parameters” tab.
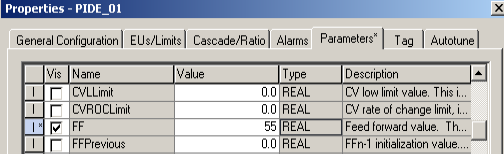
Re-Initialize the Control Variable
A different method is to re-initialize the Control Variable. Again, be aware whether your process is forward acting or reverse acting. To re-initialize the CV, go to “Parameters” and enter an “CVInitValue” for the CV. Once you enter the value, turn on the “CVInitReq” bit. Be sure to press enter, then apply for your changes to take affect. For the most part, this is similar to putting the PID into Manual mode. Find a CVInitValue that causes your PV to start to move. Once your PV is near the setpoint, you can shut off the CVInitReq bit. At this point, your proportional gain should attempt to react to the PV, and you should be able to continue tuning your PID.
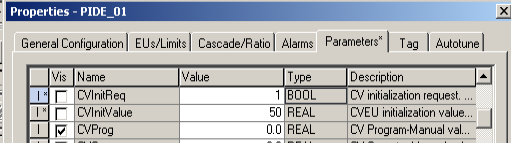
Add Integral
Obviously, we don’t know what value to enter for your integral gain. It’s OK though as long as your process cannot be harmed by incorrect values. A sensible value should cause your PV to start to move toward the setpoint. I’ve found that a good starting point for the processes I’ve worked on is around 0.1 minutes, or 6 seconds per repeat. If you have another similar loop in the plant, you can get a good idea where to set integral by copying it’s values. Pay attention to the units of your PID. Once the PV starts moving toward the setpoint, you can shut off the integral, and resume tuning your loop.
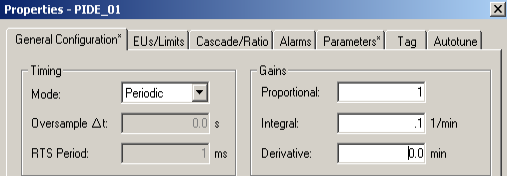
Manual Mode
Another option is to go to Manual Mode if you have that ability easily available. You can get the PV somewhere near the setpoint, and switch back to auto. I won’t go into details on that here, because there are so many different configurations that allow you to go to manual mode.
Summary of PIDE Stuck High or Low
In short, you will usually want the PV somewhere near the setpoint before tuning. You can do this with Bias (FF), Re-Initialzing the CV, by going to Manual Mode, or by adding some integral. When tuning the loop, you don’t want the PV to enter saturation at 100% or 0% during oscillations. This could affect your calculation for the best settings.
For more information, visit the ControlLogix Category Page!
— Ricky Bryce