Introduction to Successful Industrial Maintenance Training
In this section, I will discuss some tips for Successful Industrial Maintenance Training. Let’s face it, training is expensive. Not only do you have the cost of the training, but also, you are paying the employees to be trained. Additionally, if they need to travel, you will also be paying for the travel expenses. You don’t want to waste these funds on training that has little benefit. Additionally, if they are not trained properly, then their lack of knowledge is far more expensive in the long run. A false sense of being trained properly can even be hazardous. I’ve compiled a list of some topics for consideration when choosing the source for your training.
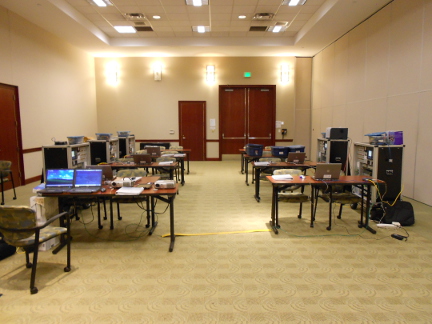
Customized Training
When choosing a source for your training, customized training is usually the best option. Customized training requires all attendees of the course to be from the same corporation, though. That way, the instructor can go over your own plant schematics, and use your own plant programs. In a typical seminar-type environment, this is usually not possible because of non-disclosure issues. Your students will get a canned course with material that may or may not apply directly to what they need to know. At any rate, the students are not seeing how the training applies directly to their own equipment. This makes it difficult for the students to visualize how the training applies to them.
On-Site Training
If you have enough students at your plant site, you can set up training at your own location. In this case, when a question arises about a particular piece of equipment, the resources to answer the question are readily available. Additionally, the instructor can walk the students onto the plant floor to point out exactly how that they are learning applies to their own equipment. Students will retain information better if they can see how every topic of the course applies directly to what they need to know.
Hands-On
Most of the course should be hands-on. This even applies to the lecture time. As the instructor speaks, the students should be able to physically identify and understand how every part of the discussion relates to the hardware. The students will also need need plenty of lab time, which allows them to work together while troubleshooting, and adding instructions to understand how they function.
The equipment in training won’t always be exactly the same as what you have in your plant. It should be close enough, though, that the student will understanding what he’s looking at when troubleshooting their own systems. For example, if you use 1756-L72 processors in the plant, and the training equipment has an L71, the difference is negligible as far as how they operate.
Programming / System Design
Most students need to be trained on how to troubleshoot and repair existing systems. If an instructor is teaching program design techniques, they might not be on track with your training needs.
Students will need to enter instructions into the processor to observe how they work, of course. However, they usually don’t need to know how to design an entire system. Unless you are training engineers who will be writing programs, and designing systems, it’s best to stick with courses that concentrate on troubleshooting.
Keep in mind that you don’t want the class to turn into a sales-pitch either.
Plant Safety
With on-site training, the instructor and students can freely discuss the safety protocols that you are using at your own location. Additionally, the class will discuss past safety incidents, and how to avoid them in the future. Additionally, the instructor is usually experienced and has seen issues at other locations. This enables the instructor to discuss possible safety hazards that would otherwise go unforseen.
Money Back Guarantee
A good training company will have a money back guarantee. Obviously, this gives the company a good incentive to do an outstanding job of meeting your training needs. If you are not happy with the training, the instructor will end the class, and pack up. No questions asked. Not only do they need to get paid for the class, but they will also want your repeat business. A money back guarantee is a great indication that the training company has a lot of confidence in their instructors!
Folow-Up Course for Successful Industrial Maintenance Training
After training, the students will have a good understanding of the plant equipment. This will lead to more questions in order to develop a full understanding of your plant systems. A follow up class on the next level of training is very useful. This enables the students to learn the equipment in more detail. Additionally, it gives them the chance to ask questions they’ve come across since attending the previous course. I would recommend having a Level 2 class three to six months after a Level 1 class.
Follow-Up Exercises
Not all of the students will have the chance to use their new knowledge right away. It’s important to periodically look at the plant schematics and trace logic in a program to retain their knowledge. It’s important to set aside some time each month for these follow-up exercises. Sometimes, it can be difficult to find time, but 30 minutes a month is much less costly than system downtime. If they maintain and grow their knowledge, students will have the ability to locate the cause of failures quickly. Maintaining their knowledge will also give them confidence when they approach a problem in your plant. This ensures less frustration, and usually, fewer mistakes.
Summary of Successful Industrial Maintenance Training
In short, choose a training company that will train your employees on what they need to know. Not only should the instructor have experience and knowledge, but they must also have the ability to train. Most instructors have one or two of those qualities, but it’s rare to find an instructor with all three!
— Ricky Bryce